Micro reduction moto contains to a variety of
plastic gear, such as plastic helical gear and plastic spur gear. Many people do not understand the difference between the helical gear and spur gear corresponding to the plastic mold processing method. Here, the engineer of Forwa plastic gear factory tell you one by one.
- plastic mould processing method of plastic spur gear, for plastic spur gear, its corresponding to plastic mold core are internal spur gear, can take wire cutting processing, wire cutting processing core surface accuracy is good, high dimensional accuracy.
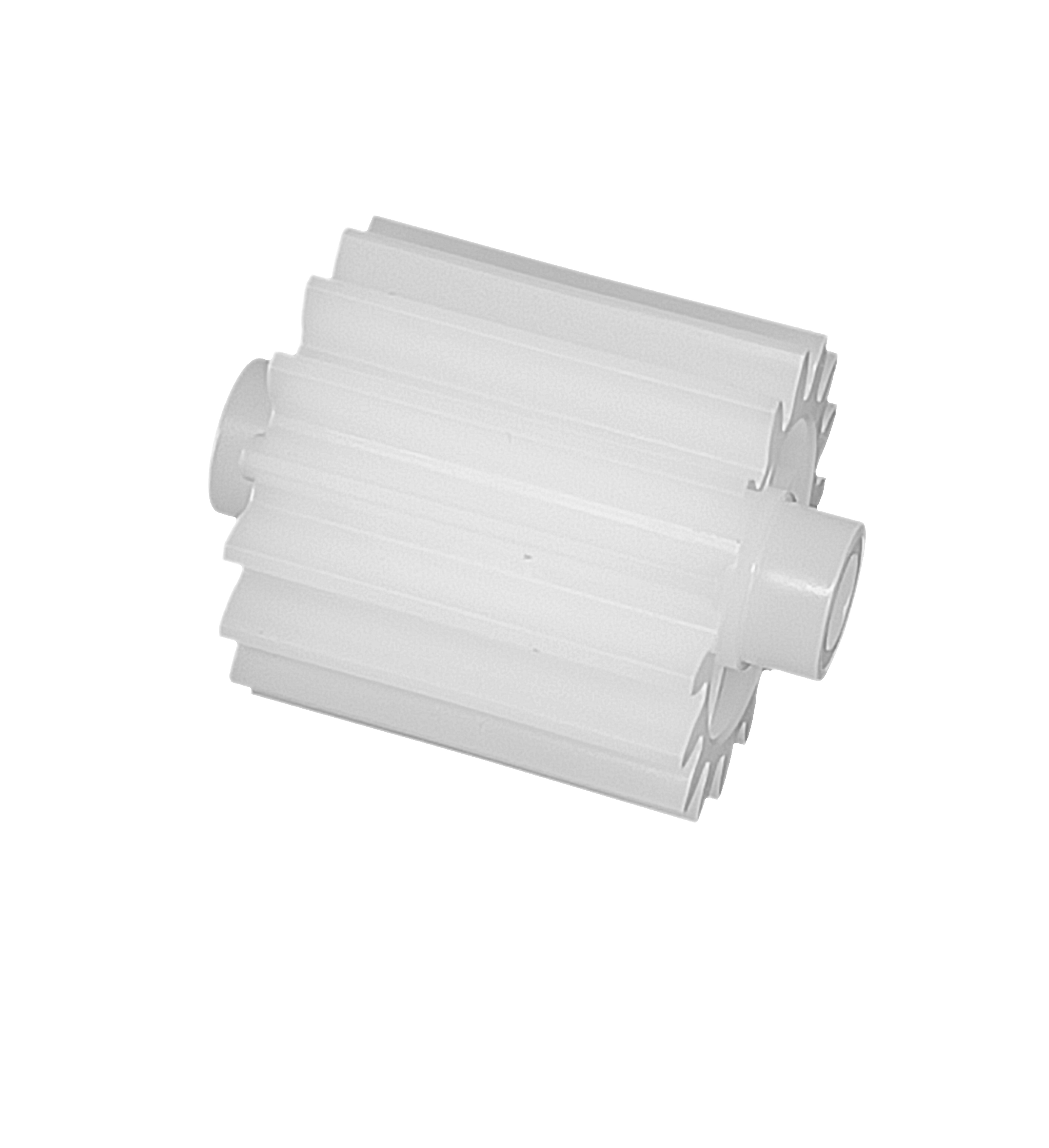
2. The mold insert corresponding to the inner ring of the plastic spur gear is the outer spur tooth. Die core inserts can be processed by wire cutting and hobbing.
3. The mold processing method of plastic helical gear. For plastic helical gear, the corresponding mold insert is a helical tooth. If the Angle is not large and the accuracy is not high, wire cutting can be used. Large Angle and high precision, through the electrode discharge processing. Discharge to use the Z axis rotation of the moto
4. The mold insert corresponding to the inner tooth ring of helical gear is the helical outer tooth. Similarly, those with small Angle and low precision can be processed by wire cutting. The helical gear with high gradient and high precision should be hobbing. It should be noted that when the helical gear die core is hobbing, the die core material should be prehardened, and the material hardness is below 40HRC.
5. The above discussion is the processing method of gear mold. From the injection Angle of gear to consider, the processing method of helical gear and spur gear are also different.
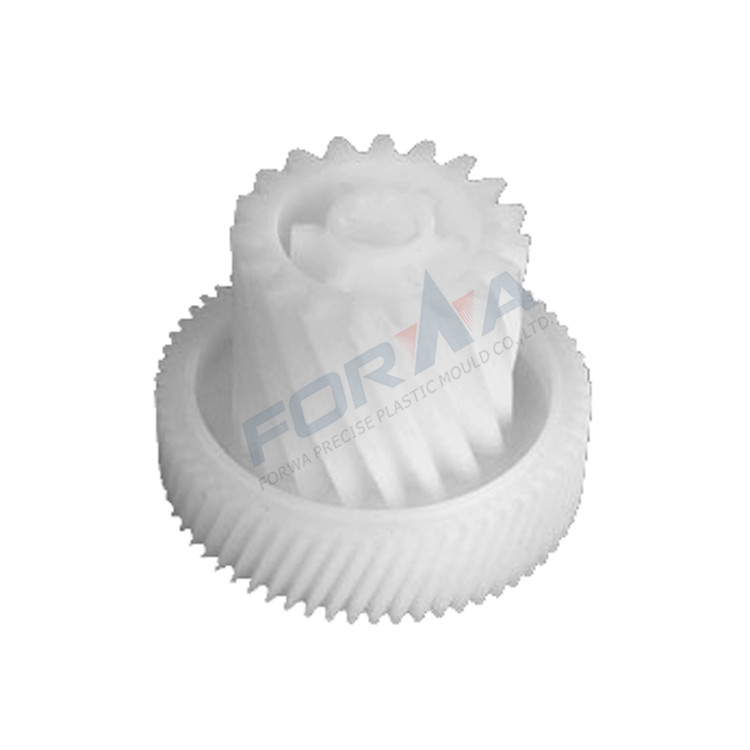
6. Spur gear is directly ejected with a thimble. Helical gears often use rotary ejection or forced ejection release. In the process of rotation, the tooth shape will be squeezed, and the gear precision is not easy to control.